State of the Art Rockets
There’s a simple reason why we hear a lot more about cars, ships, and planes than we do about rocket ships: there are a lot more of them. In addition, while each flight into space does have a small impact on the planet it leaves behind, for the moment, at least—these launches are very rare. Only a couple of rockets blast off every week around the world, but soon, the number of launches will increase, and this problem will grow in importance rapidly.
First, let’s understand how a rocket works: of course, it is obvious that the higher the thrust, the less time a rocket can fly. That’s why during a launch, we see the first stage pushing for a very short time (around 600 seconds) before being detached. (example of SLS static fire test).`
Most rockets fall into two categories: solid rocket motors and liquid rocket motors, based on their construction and fuel type.
We also must understand that there are basically two families of large rockets. The first one is solid rocket motors. These are more commonly used in first stages and are like having a solid amount of propellant ready to burn whenever it is turned on. As you can imagine, it provides a lot of thrust, but it’s highly explosive, like a C4 charge .
So, if you happen to be near a launch ready rocket, I suggest you avoid having a barbecue!
The second is the liquid rocket motors family. Highly pressurized fuel and oxidizer are pumped in a combustion chamber and burned together. These engines are those which can drive the second stage of a rocket in space. The thrust provided is less because, as you can imagine, liquids have a lower energy density than solids do on average, but their advantage is that they can burn for a much longer time.
Engineers struggle to find the best compromise to have a rocket that can be fired for a longer time while providing a huge amount of thrust. And of course, this needs to be done at the lowest cost possible.
Performance at a Cost
Performance hardly comes free of charge. In fact, propellant is often one of the costliest parts about rocket building. So, it’s an issue that needs to be tackled properly for the cost of rocket building to come down a reasonable amount.
In this case, it is useful to analyze fluorine-powered rockets. The idea of implementing fluorine in rocketry goes back to the edge of the space exploration era. The element provides the highest-performing combination. However, we rarely see it nowadays given that overly focusing on performance alone is a naïve and over simplistic approach to development costs. Applying the logic above, we must consider the cost of acquiring and maintaining the propellant and the associated risks. As economists often argue, risk and cost always dance together.
To begin, fluorine needs to be stored and used in its liquid state. The temperature at which elements have specific states differs from one another, and for fluorine, condensing happens at –188 °C. The costs needed to sustain this, in the long run, are extremely high compared to other solutions, not to mention the effort required in terms of logistical expenditures. In 1959, NASA estimated a cost per Kilogram of $6.00 for fluorine, against a mere $0.04 for liquid oxygen. Undeniably, this generates a burdensome externality in the form of environmental impact when a lot of energy is consumed.
Furthermore, liquid fluorine is extremely toxic and unstable. Fluorine is the most powerful oxidizer known and it only takes one spare electron from another element to trigger a Hollywood-worthy explosion. In the lower atmosphere, when we combine it with liquid hydrogen, oxygen and water vapor, hydrofluoric acid is created as a by-product, which is not really a desirable outcome. This translates into higher costs to avoid such a scenario, and in turn, a stronger impact on the environment.
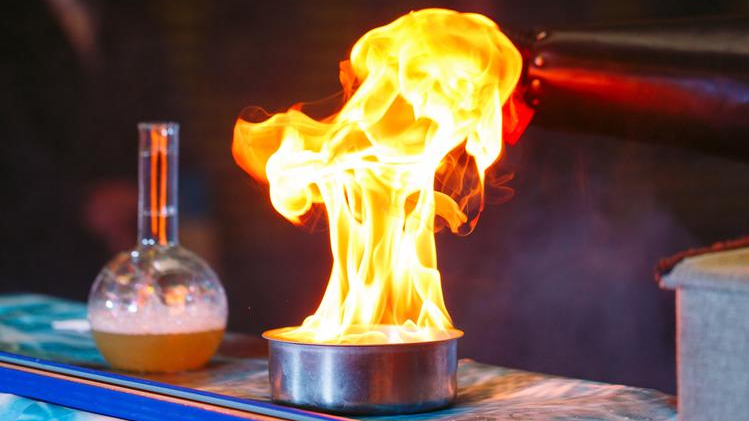
A fluorine gas fire demonstration
The case of fluorine is very helpful to understand how wide the spectrum of evaluation is when we assess new solutions for propellants. To understand the real impact of different compounds and technologies, it is essential to avoid focusing on the launch phase itself. Much harm can stem from the production and the logistic phases, and a superficial analysis that does not take these into account can only produce weak results carrying no value at all.
Environmental Background
Pushing the limits of performance often includes complex chemical reactions. In solid rocket motor development, metal (aluminum) is often added in the propellant to increase its performance. The physics behind this is clear: if we expel something heavier, the thrust we receive is higher. The main problem, however, is that tons of particles of aluminum, carbon dioxide, and soot are released into the atmosphere. These are reactive gases that cause environmental degradation, such as ozone molecules to breaking apart. To make matters worse, spacecraft dump these pollutants directly into the upper and middle stratosphere, where they can start causing damage immediately.
On the other hand, liquid fuel seems to be more environmentally friendly since it provides a “cleaner” and more controllable flight, and their burn results in the emission of less harmful chemicals. Mostly, these are CO2, water vapor, and less harmful oxides. Therefore, liquid rocket boosters can be considered the “greener” approach. But a challenge remains. The number of rockets launched has been multiplied by the growth of interest in the sector and the advancements in the industry. Thus, the environmental impact of the modern era space race still has a very big impact on the global effort against climate change.
Thus, the question remains: What can we do in order to launch rockets without straining on the environment? The answer for the time being is simple: we must regulate the limits of chemical exhaust in the atmosphere depending on the size and weight of each rocket. We also should promote the use of a single rocket for launching multiple satellites. In that way, both the cost and the emissions would be reduced in comparison with multiple rocket launches.
Liquid rocket motors are considered the more environmentally friendly option, but they have their own environmental drawbacks.
Low-cost Production
Significant cost reduction could be achieved by using the lower priced components. Although it may seem that lower priced materials lead to worse performances, that is not always true. Major industry players speculate a lot on the cost of components, so using lower priced ones is a solution where you can use the same value to get a revised total price system. Considering that a complete rocket made with these materials could cost about $600,000, this would be a significant saving from the $4M current rockets cost, where the propulsion system by itself costs almost 20% of the total.
Another emerging idea in the last decades is reducing the manufacturing cost of rockets by using 3D printers. For instance, Rocket Lab, a Silicon Valley-funded space launch company, launched the maiden flight of its battery-powered, 3D printed rocket from New Zealand. The company’s emphasis is to develop a reliable launch vehicle that can be manufactured in high volumes with the goal to make space obtainable by providing exceptional frequency of launch opportunities, using their Electron vehicle. The mission also met its objective: making it to space. Meeting the objective was an important milestone in the commercial race to lower financial and logistical barriers to space.
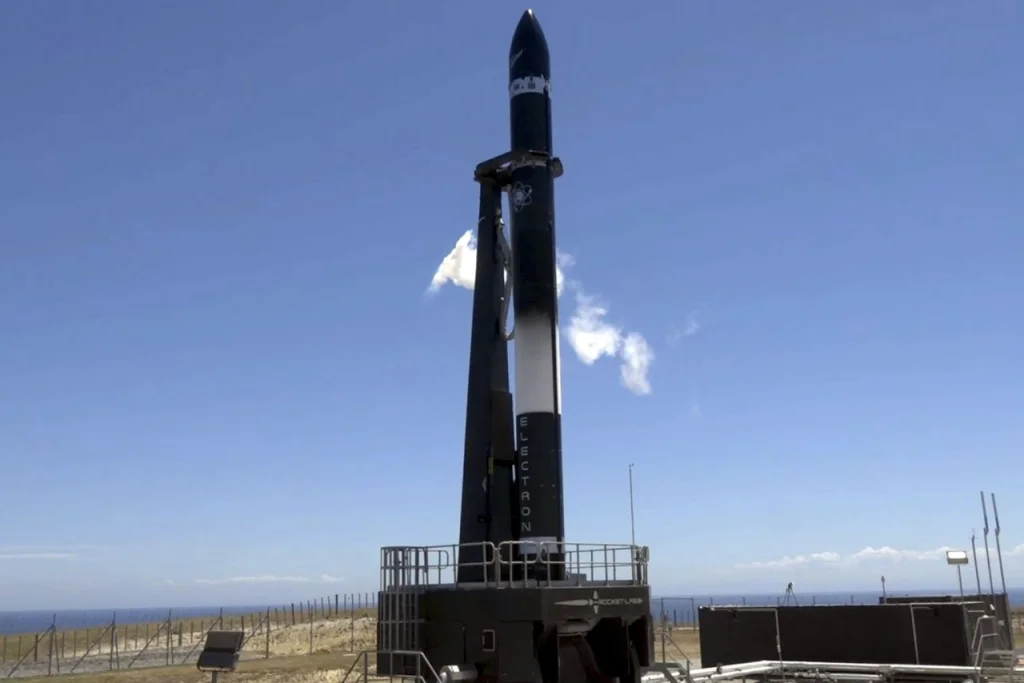
Rocket Lab’s Electron rocket sitting on its launch pad in New Zealand, 2020
The Business of Space
Furthermore, an American company based in Los Angeles, Relativity Space, has built the world’s largest 3D metal printer called Stargate for use in creating rockets. The printer, which uses sensors and function-based learning to print rockets made of stronger more reliable alloys, will redefine how we go into space, reducing the window between launches to a couple of days. “This 3D printed technology is a game-changer when it comes to reducing total hardware manufacturing time and cost,” says Tom Teasley, test engineer at NASA’s Marshall Space Flight Centre. Their first launch is scheduled for later in 2021.
The future path of the space industry will be dictated by environmental limits and start-ups are emerging to tackle them. Solutions range from creating new fuel compounds to even introducing a new, more sustainable engine.
Regarding the former option, Skyrora is a company which is currently working on a rocket fuel named Ecosene. They aim to convert non-recyclable plastic waste into high-grade in-demand rocket fuel. To do this, they are working on an innovative plastic recycling method through catalytic pyrolysis to produce energy and high-quality fuels for the aerospace industry. With an increasing need to manage global waste and growing demand for fuel, the production of Ecosene rocket fuel could change the industry in years to come. Results already showed that Ecosene is 1-3% more efficient than kerosene.
Technology for Propulsion and Innovation is another firm creating a sustainable space industry. They are working on a simple, versatile, and cost effective bi-propellant propulsion system to provide mobility to satellite platforms and microsatellite deployers. The system is specifically conceived to represent a tradeoff between costs and performances, targeting a substantial cost reduction with respect to currently available bi- propellant units. Regarding sustainability, their solution (hydrogen peroxide) is basically hydrogen and oxygen, meaning that its by product is water. It also allows for reduced compatibility issues since their solution “explodes less often” thanks to a better interface with kerosene, the usual fuel we get every day at the gas station with our car.
0 Comments