Introduction
As humanity ventures deeper into the cosmos, we stand on the brink of a transformative era marked by in-space manufacturing, a potential game-changer in the healthcare and technology sectors. This article explores these advancements comprehensively reviewing the most recent progress in the field including complex protein structures production, bio-fabrication of organic materials, construction of satellites in orbit, and cost-effective fabrication of semiconductors.
Revolutionizing Medicine Through In-space Protein Crystallization
The first field that has greatly benefited from the development of in-space manufacturing is medicine and in particular protein crystallization. Proteins are pivotal to human health, serving as the fundamental building blocks of life and playing various crucial roles within our bodies. Understanding the structure of proteins associated with specific health conditions can significantly aid scientists in developing innovative approaches to prevent and treat diseases. Determining a protein’s structure involves crystallizing the protein, followed by using techniques such as X-ray diffraction or neutron diffraction to decode the precise arrangement of atoms within the crystal. However, gravity-induced phenomena like sedimentation and convection currents on Earth can distort the growing crystal structures, leading to imperfections and hindrances in subsequent structural analysis. Thus, microgravity environments have a major advantage in this field of research.
Historically, the unique conditions on the Space Shuttle and Mir programs offered scientists a novel environment to grow protein crystals. Researchers found they could produce protein crystals of superior quality in microgravity compared to those on Earth. This advantage stems from the lack of gravity, which allows the crystals to grow uninhibited by the need for structural support, enhancing their integrity and quality. Since its inception over two decades ago, the International Space Station (ISS) has carried on this tradition of in-space protein crystal growth, providing a valuable platform for this important research. With more than 500 Protein Crystal Growth (PCG) experiments conducted as of 2021, it’s no surprise that PCG research has become the most extensive category of experiments undertaken on the station. These in-space endeavors have attracted the participation of pharmaceutical companies and academic researchers, further validating the value and potential of this research.
For instance, the high-quality protein crystal growth project initiated by The Japan Aerospace Exploration Agency (JAXA) in 2002 has enabled significant progress. Known as JAXA PCG, this project utilizes the unique environment of the ISS to foster the growth of protein crystals. Proteins and optimized crystallization solutions are carefully loaded into JCB-SGT crystallization bags and transported to the ISS via Soyuz capsules. Upon arrival, these precious cargoes are placed into an incubator to maintain a constant temperature. Throughout the experiment, ground controllers diligently monitored and adjusted the temperature as required. The proteins are incubated and crystallized in space for one to two months before being returned to Earth aboard a Soyuz or Dragon spacecraft.
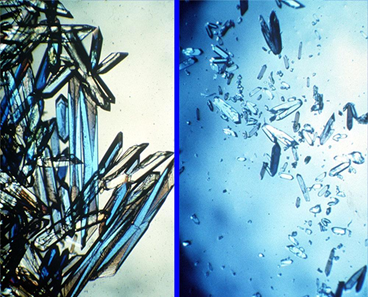
Microgravity helps to grow bigger crystals. |
The outcome of these space-faring experiments can propel research to exciting new horizons. For instance, the superior-quality crystals of disease-causing proteins grown in space could enable scientists to determine the protein’s structure accurately. With this enhanced structural understanding, they could design a new drug specifically tailored to interact with the protein, paving the way for advanced therapeutics. Hence, in-space protein crystallization experiments offer tremendous potential for advancing biomedical research and drug development. In addition to protein crystallization, in-space research can revolutionize another field of biology: bio-fabrication of organic materials.
Creating New Opportunities for Bio-fabrication
Bio-fabrication represents an exciting frontier in biotechnology, defined as creating intricate biological products from foundational materials such as living cells, extracellular matrices, biomaterials, and bioactive molecules. The advent of 3D fabrication technologies has notably propelled this rapidly advancing field. These raw materials, vital for bio-fabrication, generate bio-ink, a substance designed for 3D bioprinters to fabricate complex living tissue.
In the future, space experiments could revolutionize the domain and enable breakthrough progress. Microgravity enables bio-fabrication of tissue and organ constructs of more complex geometries, thus facilitating novel scaffold technologies based on multi-levitation principles. Furthermore, fabricating dated tissues exposed to space’s microgravity and cosmic radiation provides an extraordinary opportunity to study unique pathophysiological phenomena. These insights are anticipated to be invaluable not only for terrestrial medical advancements but also for the safety and health of astronauts on extended space missions.
NASA’s Bio-Fabrication Facility |
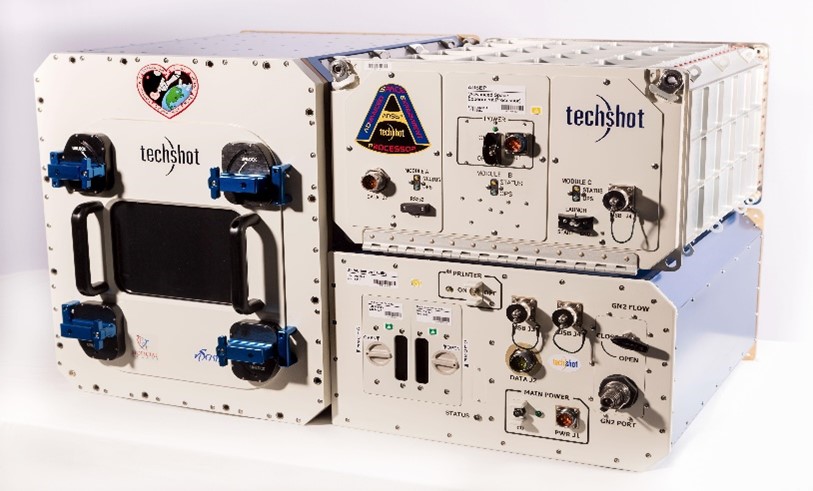
One of the significant potentials of 3D bioprinting lies in its capacity to address the escalating issue of organ transplant shortages. With an increasing demand for organ transplants and a persistent lack of sufficient organ donors, 3D bioprinting, if successfully implemented, could revolutionize regenerative medicine. By employing a patient’s cells as the foundation for the bio-ink, science-ink could c an entire organ simply by printing it. This approach offers substantial benefits. The resulting organ, derived predominantly from the patient’s tissue, would circumvent the issue of organ rejection since it would not elicit a robust immune response.
Additionally, 3D-printed organoids—small, simplified versions of organs—could serve as invaluable tools for doctors and medical researchers. These organoids could be employed to model disease processes, test new drugs, and propel the medical field forward. As such, 3D bioprinting promises to unlock unprecedented advancements in personalized medicine, organ transplantation, and our overall understanding of human health.
Exploring New Horizons with In-Space Built Satellites
In-space manufacturing holds potential in medical applications and offers significant advantages for other domains, such as satellite construction. With over a thousand satellites of Earth origin currently in space, these devices serve diverse functions and can be broadly classified into two types: communication and observation devices. Communication satellites act as sky-based antennas, transmitting radio and television signals between distinct areas on Earth, thereby “illuminating” specific parts of the globe. On the other hand, observation satellites are designed to gather data and information. Creating a satellite demands significant resources, mainly due to the materials necessary for manufacturing, each intended to meet stringent specifications. Satellites must be durable enough to withstand space radiation and pressure changes in the space environment and possess the strength to resist potential impacts from space debris or minor asteroids.
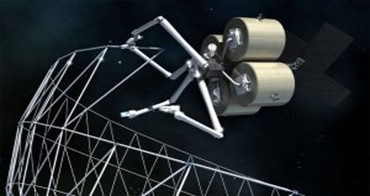
NASA’s Bio-Fabrication Facility |
However, what becomes of these satellites when their operational life is exhausted? A satellite typically has a functional lifespan of between 5 and 15 years. Engineers can use their remaining fuel to decelerate them for closer satellites, causing them to deorbit and incinerate the Earth’s atmosphere. Alternatively, the satellite can be propelled further away from Earth. A remarkable instance of this is the twin Voyager 1 and 2 spacecraft. Launched from Cape Canaveral, Florida, in 1977, these spacecraft are in uncharted territory, much farther away from Earth and the sun than Pluto. Voyager 1 officially entered interstellar space on August 25, 2012, with Voyager 2 set on a similar course. Both spacecraft continue to study ultraviolet sources among stars and investigate the boundary between the Sun’s influence and interstellar space. They are expected to transmit invaluable data for at least another decade, maintaining communication until their power sources can no longer sustain critical subsystems. Along with the construction of satellites, in-space manufacturing will also unleash its potential with the production of semiconductors.
Improving Semiconductors Through New Fabrication Processes
The production of semiconductors on Earth represents a significant challenge, and the industry may greatly benefit from some advantages induced by space environments. Semiconductor wafers demand substantial volumes of ultrapure water to maintain material purity. This necessity considerably escalates the production cost. Owing to the microscopic scale of semiconductors and associated products, any particulate matter contaminating the water could cause irreparable harm, leading to product rejection. To reach ultra purity, the water must be meticulously purified, removing even organic carbons, which serve as nutrition for bacteria that could further compromise the water. Removing silica molecules is also imperative, depending on the wafer size under production. As semiconductor designs grow more intricate and their sizes shrink, the purity standards consistently elevate. The ultrapure water specification 2001 defined acceptable particle sizes at 65 nanometers, a benchmark that has steadily reduced since.
|
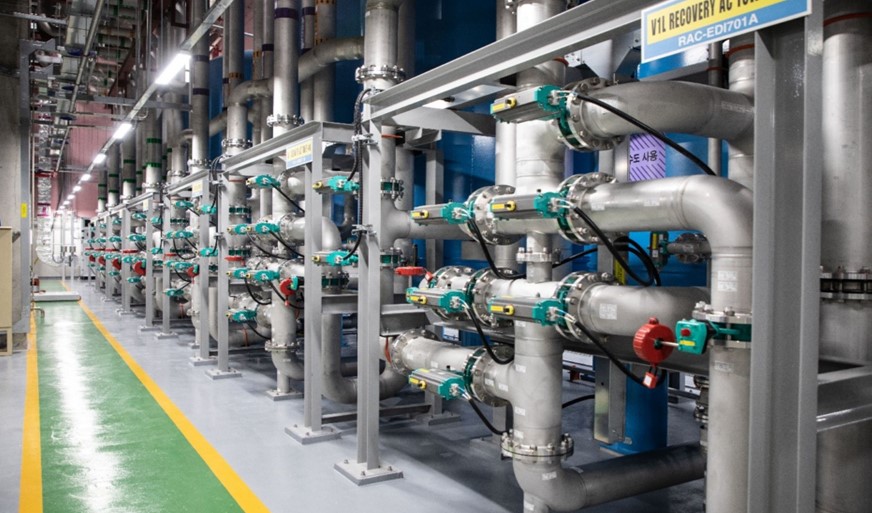
Conversely, the naturally sterile and ultraclean conditions in space drastically curtail the requirement for ultrapure water. In the vacuum of space, wafer production by atomic layering—known as sedimentation—can occur without contamination concerns. The usage of ultrapure water is significantly reduced, and the production costs correspondingly plummet with advancements in these technologies. The hazardous waste resulting from the conventional terrestrial process presents costly and complex disposal challenges, issues practically nonexistent in space. The in-space assembly of semiconductors follows an epitaxy process; materials are deposited in minute layers sequentially onto a substrate within a vacuum chamber. The deposit usually forms a crystal or a thin film. The substrate is crucial, as it dictates the efficiency of deposit material growth and influences the structural integrity of the resulting deposit. This step-by-step process ultimately yields the semiconductor wafer. The technological breakthrough also reshuffles semiconductors geopolitics and has a significant economic and political impact on a world scale.
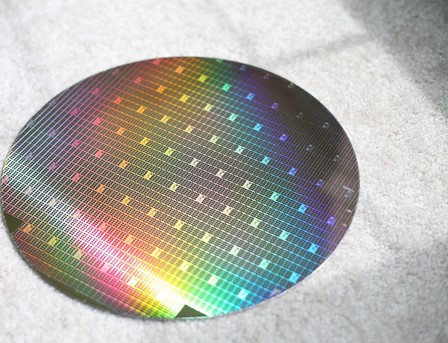
|
Presently, East Asian economies, notably Taiwan, South Korea, and Japan, dominate the global semiconductor manufacturing sector due to the volume and quality of their production. The United States is the only country with a significant Western semiconductor industry.
This geographic concentration in East Asia affords these countries considerable power, given the pivotal role of semiconductors. The repercussions were evident during the economic downturns induced by the COVID-19 pandemic. The enforced lockdowns reduced or halted the production of many goods, including semiconductors. Consequently, the prices of essential electronics like phones and laptops, all reliant on these technologies, soared dramatically. This situation could benefit the developing Asian economies, providing them a strategic advantage to enhance their global standing and influence during international disputes.
The entities possessing the requisite resources and technology to render in-space semiconductor manufacturing commercially viable are the USA and EU, credited to their successful space programs. Therefore, the pioneers of these innovative methods are likely to be the EU and USA. Their cost-effective production strategies could pave the way for their industry domination. This shift could potentially erode a significant portion of the bargaining power these East Asian countries have garnered through their focus on semiconductors and high-value manufacturing, such as Taiwan. This dynamic might empower the West to negotiate unfavorable trade deals with the developing East, further solidifying their position as global leaders. East Asia could witness an overall decline in economic activity as they grapple with increased unemployment. Consequently, the in-space manufacturing of semiconductors in the future may accelerate the transition from a manufacturing-centric economy to a services-based model.
Authors: By Teodora Stefan, Giulia Amenduni, Charvak Thatha
0 Comments